Industria 4.0 prende il nome dall’iniziativa Europea Industry 4.0, a sua volta ispirata ad un progetto del governo Tedesco. È un processo che scaturisce dalla quarta rivoluzione industriale e che sta portando alla produzione industriale del tutto automatizzata e interconnessa.
Le nuove tecnologie digitali avranno un impatto profondo nell’ambito di quattro direttrici di sviluppo:
La prima riguarda l’utilizzo dei dati: la potenza di calcolo e la connettività, e si declina in big data, open data, Internet of Things, machine-to-machine e cloud computing per la centralizzazione delle informazioni e la loro conservazione
La seconda è quella degli analytics: una volta raccolti i dati, bisogna ricavarne valore. Oggi solo l’1% dei dati raccolti viene utilizzato dalle imprese, che potrebbero invece ottenere vantaggi a partire dal “machine learning”, dalle macchine cioè che perfezionano la loro resa “imparando” dai dati via via raccolti e analizzati.
La terza direttrice di sviluppo è l’interazione tra uomo e macchina: che coinvolge le interfacce “touch”, sempre più diffuse, e la realtà aumentata.
Infine c’è tutto il settore che si occupa del passaggio dal digitale al “reale” e che comprende la manifattura additiva, la stampa 3D, la robotica, le comunicazioni, le interazioni machine-to-machine e le nuove tecnologie per immagazzinare e utilizzare l’energia in modo mirato, razionalizzando i costi e ottimizzando le prestazioni.
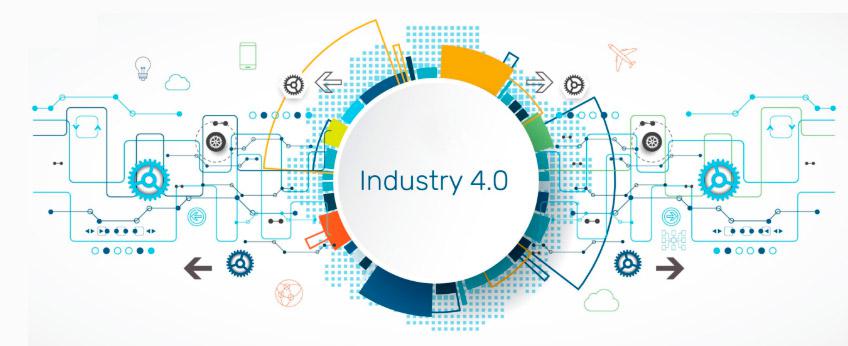
REQUISITI NECESSARI
Ecco una catalogazione dei Beni:
Beni strumentali il cui funzionamento è controllato da sistemi computerizzati o gestito tramite opportuni sensori e azionamenti.
Sistemi per l’assicurazione della qualità e della sostenibilità.
Dispositivi per l’interazione uomo macchina e per il miglioramento dell’ergonomia e della sicurezza del posto di lavoro in logica «4.0».
Beni immateriali (software, sistemi e system integration, piattaforme e applicazioni) connessi a investimenti in beni materiali «Industria 4.0.
I macchinari devono essere:
- controllati per mezzo di CNC (Computer Numerical Control) e/o PLC (Programmable Logic Controller).
- interconnessi ai sistemi informatici di fabbrica con caricamento da remoto di istruzioni e/o part program.
- integrazione automatizzata con il sistema logistico della fabbrica o con la rete di fornitura e/o con altre macchine del ciclo produttivo.
- interfaccia tra uomo e macchina semplici e intuitive.
- rispondenza ai più recenti parametri di sicurezza, salute e igiene del lavoro.
Inoltre tutte le macchine sopra citate devono essere dotate di almeno due tra le seguenti caratteristiche per renderle assimilabili o integrabili a sistemi cyberfisici:
- sistemi di telemanutenzione e/o telediagnosi e/o controllo in remoto.
- monitoraggio continuo delle condizioni di lavoro e dei parametri di processo mediante opportuni set di sensori e adattività alle derive di processo.
- caratteristiche di integrazione tra macchina fisica e/o impianto con la modellizzazione e/o la simulazione del proprio comportamento nello svolgimento del processo (sistema cyberfisico).
PERIZIA TECNICA
E’ ammessa la possibilità di produrre l’eventuale perizia / attestazione di conformità in due fasi separate e successive:
- La prima, basata sulla verifica dei requisiti tecnici del bene
- La seconda, a buon esito della verifica dell’avvenuta interconnessione
La due fasi possono essere così organizzate:
- Prima fase, preliminare: Basata sulla verifica dei requisiti tecnici del bene, eventualmente presso il produttore; in linea di massima questa fase può essere condotta anche prima dell’acquisto del bene;
- Seconda fase, conclusiva: Comprende il sopralluogo presso l’utilizzatore per la verifica del bene nelle condizioni operative; questa fase deve essere condotta quando il bene è installato e pienamente operativo, ed interconnesso.
- Solo il risultato della seconda fase potrà essere utilizzato per l’ammissibilità del bene ai benefici fiscali (ad esito positivo)